하이네켄, 멕시코 공장 중단되자 재빨리 네덜란드로 거점 변경
도요타, 반도체 4개월치 축적해 공급망 문제 탈피
맥킨지 "기업 55%, 공급처 최소 2곳 확보 노력"
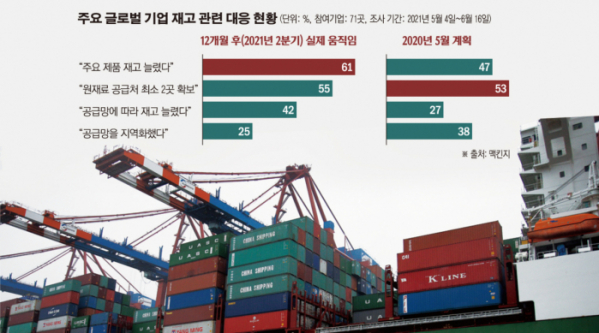
과거 기업들은 ‘적시 생산(Just In Time)’ 공식에 기반을 둔 공급망 관리 시스템을 운영했다. 하지만 이제는 만약의 사태에 대비하는 것에 초점을 맞춘 ‘상황 대비(Just In Case)’ 방식으로 전환하는 추세다.
파이낸셜타임스(FT)에 따르면 190개국에 300개의 브랜드를 판매 중인 맥주 업체 하이네켄은 지난해 멕시코에서만 생산하던 도스 에퀴스 브랜드를 놓고 난관에 봉착했다. 멕시코 정부가 코로나19 기간 맥주를 비필수품으로 분류하고 양조장을 일시 폐쇄했기 때문이다. 자칫 해당 브랜드 공급이 아예 가로막힐 위기였지만, 하이네켄은 라벨과 병을 네덜란드로 보내 새로운 양조 거점으로 삼았다. 이후 멕시코 공장이 가동을 재개했지만, 업계에선 대체 생산 거점의 필요성이 대두됐다.
지난 수십 년간 기업들은 공급망 업체를 선택하고 공장을 건설하며 재고량을 결정할 때 무엇보다 비용을 중시했다. 이런 철학은 재고를 최소화하고 수요 변화에 빠르게 적응할 수 있는 단기적이고 유연한 움직임을 강조하는데, 이게 바로 적시 생산이다.
컨설팅그룹 KPMG의 브라이언 히긴스 미국 공급망 책임자는 “오늘날 우리고 보고 있는 무너져 내린 공급망 상당수는 20년 전 당시엔 보편적인 진리에 근거해 굳어진 모델”이라며 “그건 리스크가 아닌 비용에 초점을 맞추고 있었기에 매우 긴 공급망이었고, 우린 거기서 일어난 균열을 여러 번 봐왔다”고 설명했다.
그러나 팬데믹 사태로 기존 공식이 더는 작동하지 않게 되자 기업들은 만약을 대비한 재고가 필요하다는 인식을 갖기 시작했다.
특히 반도체 공급 문제에 직격탄을 입은 자동차 업계에서 이 같은 움직임이 뚜렷하게 보인다. 대표적인 사례가 도요타자동차다. 지난해 미국 시장에서 제너럴모터스(GM)의 100년 아성을 누르고 연간 자동차 판매 1위를 기록한 도요타는 적시 생산에서 탈피한 성공 사례로 평가받는다. 과거 부품이 필요할 때 공장에서 바로 생산하는 방식을 채택했던 도요타는 코로나19 발생 후 차량에 사용되는 컴퓨터 반도체 4개월 치를 사전에 비축한 덕분에 반도체 공급 피해를 줄일 수 있었다.
포드와 GM 역시 칩에 대한 접근성을 개선하기 위해 반도체 업체들과 기존의 단순 공급 계약이 아닌 파트너십을 구축하기 시작했다. 맥킨지의 최근 설문조사에 따르면 지난해 2분기 응답 기업의 61%가 주요 제품 재고를 늘렸고 55%는 최소 두 곳 이상의 공급처를 확보하기 위해 조처한 것으로 집계됐다.
운송기업 UPS의 캐롤 톰 최고경영자(CEO)는 “기업들이 좋아하는 건 운전자본의 최적화”라며 “따라서 과거 많은 제조업체는 재고를 적시에 조사했고, 시스템은 상당히 잘 작동했다”고 말했다. 그는 “하지만 대유행 여파로 제조업을 포함한 모든 게 중단된 상황에서 경제가 개방되기 시작하자 수요는 급증했다”며 “적시에 재고를 마련하는 건 더는 효과가 없었다”고 지적했다. 이어 “지금 기업들은 ‘만일을 대비해서’ 재고가 필요하다고 생각하고 있다”고 덧붙였다.
그 결과 현재 많은 나라에서 창고 비용이 급격히 증가하는 추세다. 부동산서비스기업 CBRE가 미국 전역과 일본 도쿄, 홍콩, 아일랜드 더블린 등 주요 도시 창고 비용을 조사한 결과 지난해 최소 5%에서 최대 15%까지 비용이 증가한 것으로 나타났다. 사용 가능한 창고를 나타내는 미국산업공실률은 지난해 3분기 3.6%를 기록해 역대 최저를 기록하기도 했다.
DHL의 오스카 드 보크 공급망 부문 CEO는 “공급망이 점점 복잡해지고 있고 자연재해가 더 자주 공급망을 방해하는 상황에서 기업들은 ‘적시 생산’을 손볼 필요가 있다”며 “기업들은 과거처럼 원하는 만큼만 계획을 세울 수 없다”고 설명했다.