봉형강 수출1위 경쟁력의 근간 당진제철소 가보니
철강을 ‘산업의 쌀’이라고 부른다. 우리 생활에 없어서는 안 되는 핵심 산업이다. 자동차, 조선, 해운, 항공, 건설 등 걸치지 않은 분야가 없을 정도로 대부분의 산업 경쟁력을 좌지우지한다. 국내 뿐 아니라 해외에서도 우리 철강업체들은 ‘대한민국의 저력’을 보여주고 있다. 이투데이는 보이지 않지만 세계 수출의 근간인 철강 생산 현장과 이를 발판으로 해외에 뻗어나가는 우리의 자랑스러운 제품과 기술을 6회에 걸쳐 집중적으로 살펴본다. <편집자주>
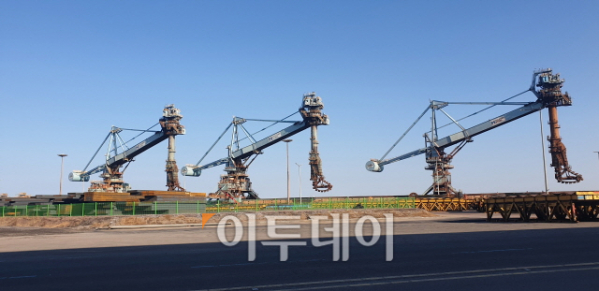
“무려 14㎞ 길이의 철로에 기차가 다니고, 공중에는 롤러코스터를 연상케하는 레일이 하늘을 휘감고 있다.”
디즈니랜드의 롤러코스터가 아니다. 서울 여의도 면적(2.9㎢)의 3배에 달하는 현대제철 당진제철소에 도착하면 펼쳐지는 풍경이다.
용광로(고로)에서 만들어진 쇳물은 ‘토페도카’라 불리는 기차가 열심히 실어나른다. 철광석을 당진 앞바다에서부터 고로까지 이동시키기 위해 1.6㎞가량 이어져 끝이 보이지 않는 컨베이어벨트(밀폐형)는 그야 말로 장관이다. 미국에서 롤러코스터는 산을 넘어 석탄을 실어 날랐던 협궤철도에서 시작됐다고 한다.
2006년 11월 한보철강 인수 후 바다, 갯벌 등을 모두 매립해 만들어진 이 곳. 2010년 국내 최초로 민간 자본으로 일관제철소를 완공하고 H형강을 대한민국 최초로 생산함은 물론 봉형강 부문 세계 수출 1위를 달성한 이 곳, 당진제철소를 지난 13일 찾았다.
◇독일도 깜짝 놀란 세계 유일의 밀폐형 원료저장시설 = 당진제철소는 철강제품의 원재료인 철광석을 100% 수입해서 쓴다. 연간 2000만톤에 달한다. 수십만톤에 달하는 철광석이 벌크선을 타고 3~4일에 한 번 꼴로 당진항에 도착하는 셈이다.
2.8㎞에 달하는 부두에는 13개의 선석(접안장소)이 있다. 현대제철의 로고가 박힌 연속식 철광석 하역기가 8대가 대기 중이다.
하역기는 한번에 무려 72톤에 달하는 철광석을 퍼나른다. 1톤을 담을 수 있는 바구니가 72개가 대롱대롱 줄지어 달려있다. 이들 바구니가 물레방아 굴러가듯 쉴새없이 배안으로 들어가 철광석을 퍼내는 원리다. 하역된 원료들은 컨베이어 벨트로 이동해 보관돔에 보관된다.
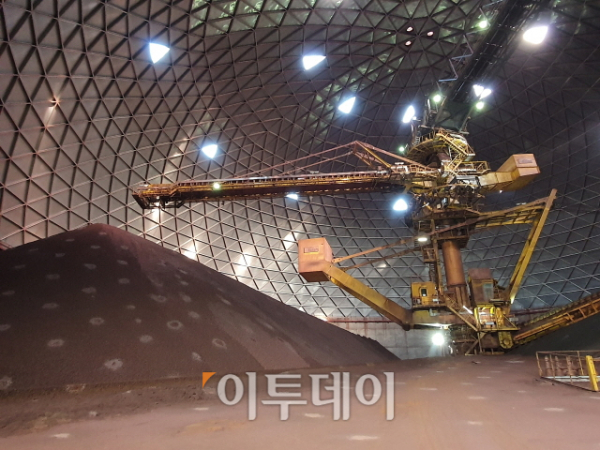
당진제철소에는 총 7개의 돔이 있다. 그 중 4개는 철광석을 보관하는 돔, 나머지 3개는 한 번에 150만 톤의 철광석을 적치하고 섞을 수 있는 배합 돔이다.
이 곳의 돔들은 세계 유일의 밀폐형 원료저장시설로 독일 포모사가 화력발전소에 적용하기 위해 벤치마킹하기도 했다.
일반적인 해외 일관제철소는 원료를 밖에 쌓아놓는다. 이 경우 바람이 불거나 비가 오면 비산 먼지가 발생해 환경 오염 일으킬 수 있다. 반면 밀폐형은 환경오염을 최소화하고 수분관리를 통해 원료를 최적화 된 상태에서 보관할 수 있다.
높이 60m, 직경 120m의 철광석 저장돔에 들어가면 천장을 뚫고 들어온 컨베이어 벨트가 가장 먼저 눈에 들어온다. 업무의 80%는 전자동화로 이뤄진다. 철광석이 돔 안으로 들어오면, 컨베이어 벨트 센서가 인식해 철광석을 떨어뜨려야 할 위치, 방향을 조정하며 적정 위치까지 이동시킨 다음 자유낙하시킨다.
보관돔 1개에는 무려 32만톤의 철광석을 한 달간 보관 가능하다. 특히 밀폐형 돔은 바닥이 좀 기울어져 있어 벽에 기대는 식으로 쌓이는 철광석은 무려 최대 31m까지 높게 적재될 수 있다.
철광석은 고로까지 연결돼 있는 컨베이어벨트를 통해 이동한다.고로에서 철광석을 녹인 쇳물(용선)은 불순물을 제거하는 제강공장까지 기차(토페도카)로 천천히 옮겨진다. 1량 당 무려 320톤을 실을 수 있으며 1530℃에 달하는 엄청나게 뜨거운 쇳물온도를 담아낸 량은 2400℃까지도 견뎌낼 수 있다.
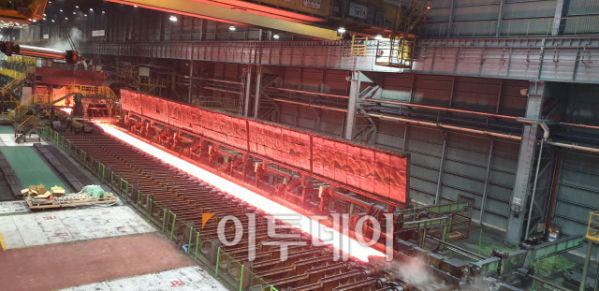
◇열연강판 1개 만드는데 3분도 안걸려 = 제강공장에서 생산된 쇳물은 연속주조 방식을 통해 중간소재(슬래브)로 만들어진 후 열연공장으로 보내진다. 철 덩어리를 더 단단하게 하기 위해 냉각과 가열을 반복한다.
당진제철소는 총 3개의 열연공장이 있다. 이 중에서 가장 큰 캐파를 갖춘 열연 2공장을 둘러봤다. 이 공장은 연간 550만톤, 하루 평균 602개 생산해 낸다. 한 개의 코일을 만드는 데 3분도 안걸린다는 의미다.
열연공장에서의 작업은 정말 순식간이었다. 식은 철 덩어리를 가열로에 넣어 1250℃에서 재가열을 한 후 압연기에서 1단계로 한 번 늘려준다. 한번만 왔다갔다 해도 최대 12m가량 되던 길이가 평균 1㎞, 최대 2.5㎞까지 늘어난다. 끝이 안보인다.
이렇게 길어진 슬래브는 보다 정밀하게 소비자가 원하는 두께와 길이에 맞게 한 번 더 압연 과정을 거쳐 105m 길이의 급속 냉각기로 연결된다. 냉각을 하면 철판이 더 단단해진다. 코일을 돌돌 마는 건치기로 이동한다. 15초면 작업이 끝난다.
열연강판보다 보다 표면이 매끄럽고 고급스러운 냉연강판 만드는 공장은 ‘철강제품의 꽃’이라 불릴 만큼 높은 기술력을 뽐냈다. 냉연공정은 말린 열연강판을 자동으로 풀어주고 식히는 작업부터 시작된다.
이어 ‘레이저 용접기’로 코일 끝과 다음 코일 처음부분을 이어준다. 염산으로 깨끗하게 목욕하고 바람으로 말린 후 상온 압연기를 거치면 다시 돌돌 말아 도금 전 단계인 중간제품(풀하드)가 탄생한다.
25톤에 달하는 풀하드는 바닥에 깔려 있는 레일 덕분에 이 넓은 공장 내에서 자동으로 이동할 수 있다. 다시 한 번 코일을 풀어서 용접, 압연, 세척을 거친다. 도금을 위한 사전작업이다. 아연 등의 도금 과정을 거치면 비로소 완제품이 된다.
◇세계 수출 1위의 산실, 연간 130만톤 생산 ‘철강공장’ = 현대제철은 철근, 형강 등 봉형강 수출을 전 세계에서 가장 많이 하는 회사다. 연간 수출 물량은 약 140만 톤으로 1조1700억 원에 달하는 규모다.
봉형강 중 연간 120만~130만톤을 생산하는 철근공장에 가봤다. 붉은 쇳물이 콸콸 쏟아져 내려오면 곧바로 냉각을 시킨다. 12m 길이의 젓가락 모양으로 자르기 위해서다. 이렇게 만들어진 80여개의 반제품(빌렛)들은 1000~1100℃의 가열로에서 뜨겁게 달궈진다.
달궈진 빌렛은 총 18단계에 걸쳐 압연을 하게 된다. 이 곳에서는 10㎜, 13㎜, 16㎜, 19㎜, 22㎜ 총 5가지 두께의 철근을 생산하는데, 일정 기간을 정해 한 가지씩 생산한다. 가장 얇은 10㎜, 13㎜는 15~18 단계에서 총 4갈래로 쪼개지며 더욱 얇아진다. 마지막 18단계에서는 흔히 볼 수 있는 일장한 간격의 마디가 생긴다.
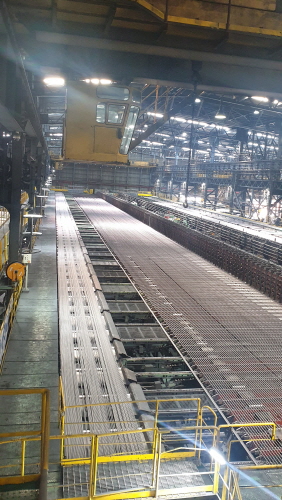
냉각 과정을 거친 후 110㎜씩 잘려진 철근들은 호위대가 한 치의 오차도 없이 행진하듯 하나씩 자동으로 옆으로 이동한다. 고객의 니즈에 맞게 잘려진 철근은 일정 무게(최대 2톤)만큼 묶어준 후 적재된다. 우리가 흔히 볼 수 있는 철근 더미다.
수 시간에 걸쳐 돌아본 당진제철소는 단순한 제조공장이 아닌 최다 세계 일류상품을 보유한 그야 말로 4차산업 혁명의 산실이었다.