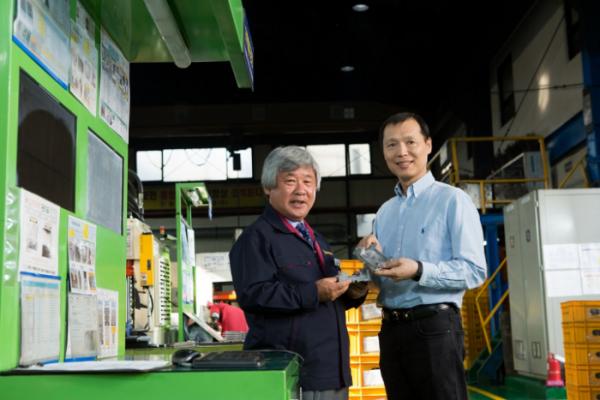
한국생산기술연구원이 중소기업 동양다이캐스팅㈜에 기술 지원해 다이캐스팅 부품의 불량률을 3%이상에서 1%대로 감소시켰다. 연간 생산비용 약 7200만 원을 절감하는 성과다.
15일 생기원에 따르면 다이캐스팅(Die-Casting)은 주조 특수 공법 중 하나로 용융된 금속을 금형에 고압·고속으로 주입하여 복잡한 형상의 제품을 대량 생산하는 뿌리기술이다.
다이캐스팅 생산 과정 중에 발생하는 불량은 크게 3가지로 나뉘는데 △금속을 녹이거나 주형에 용탕이 주입되는 과정에서 가스가 혼입되어 나타나는 ‘기포 불량’ △금속이 수축하면서 빈공간이 발생하는 ‘수축 불량’ △성형 자체가 온전하게 되지 않은 ‘미성형 불량’이 있다.
미성형 불량의 경우 육안으로도 불량이 확인되지만 기포·수축 불량의 경우 최종 QC(품질관리) 과정에서 CT(컴퓨터단층촬영)로만 내부 불량을 찾을 수 있어 공정 시간, 비용 및 인력낭비 문제가 있다. 아울러 불량품은 완제품 품질과 직결되어 기업의 신뢰도에 영향을 주는 만큼 불량률 개선이 중요하다.
주로 대기업에 알루미늄 주조부품을 납품하는 다이캐스팅 제조 전문기업인 동양다이캐스팅은 지난 2018년 ‘ECU 케이스’의 불량률 개선을 위해 생기원의 문을 두드렸다. ‘ECU 케이스’는 자동차 전장의 브레인에 해당하는 ECU(전자제어장치)에 들어가는 부품이다. 단일 품목 중 생산량이 가장 많아 하루 3600개를 생산하는데 공정상 불량률이 3%이상에 달했다. 대다수 뿌리기업이 그렇듯 MES(제조실행시스템)를 통해 DB에 제조공정 데이터를 저장하고는 있었지만, 데이터 활용 체계가 없어 공정 조건에서 불량품을 찾아내는 데 난항을 겪었다.

생기원 공정지능연구부문 황호영 박사 연구팀은 AI(인공지능)기술 적용으로 공정 조건 최적화를 통해 불량률을 낮추고, 예측 및 통제 가능한 스마트 공정 체계 구축에 성공했다. 연구팀은 공정 조건별 △군집분석 △일별 불량률 집계 △공정 조건간의 상관관계 분석 △컴퓨터 시뮬레이션을 통한 공정 최적화를 병행했다.
이를 위해 먼저 관련 데이터를 실시간으로 수집하는 환경을 구축했다. 계절별 불량 발생 변동 원인 분석을 위해 장비의 진동, 현장의 온도․습도․기압 등의 변수 측정을 위한 센서를 추가로 부착해 생산 공정상의 약 20개의 변수를 도출했다.
이렇게 수집된 데이터를 바탕으로 약 20개의 공정변수 중 불량률과의 상관관계 분석을 실시해 관련 있는 3개의 변수를 찾아냈다. 도출된 공정변수들은 컴퓨터 시뮬레이션을 통해 최적 값을 산출했다. 해당 최적 값으로 금형 방안 개선과 공정조건 설정 값을 개선해 불량률을 낮췄다. 여기에 군집분류 알고리즘을 적용해 특정 공정 조건이 주어질 때 생산부품이 양품인지 불량인지를 판정하는 기능도 개발했다. 이를 통해 99% 정확도로 양품 판정이 가능해 졌다. QC에서 불량을 찾아내던 것과 달리 생산과정에서 불량 판정이 가능해짐으로써 시간, 비용 및 인력 낭비까지 줄일 수 있었다. 불량률 개선은 기업의 이미지 제고에도 긍정적인 영향을 미칠 것으로 예상된다.
동양다이캐스팅 오경택 대표는 "기술적 난제를 극복하는 데 생기원이 큰 힘이 됐다"며 "많은 중소기업들이 생기원을 부설 연구소처럼 활용했으면 좋겠다"고 말했다.
생기원 황호영 박사는 "앞으로도 동양다이캐스팅을 비롯한 중소기업들과의 협업을 통해 생기원의 역할과 임무를 다할 수 있도록 노력하겠다"고 말했다.