전자동 터미널 하역시스템, 年 하역능력 630만 TEU 확대 계획
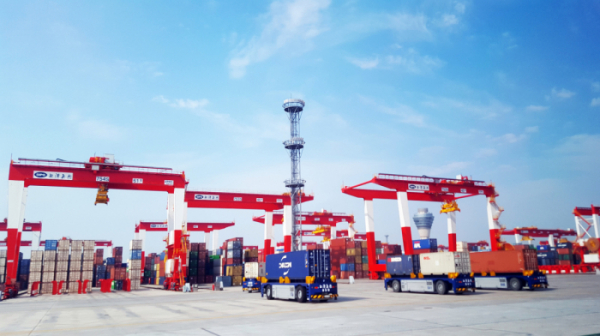
의아했다. 우리나라가 기술력을 배우러 중국에 간다니. 그것도 세계에서 한국이 인정받는 정보기술(IT) 분야를.
의구심은 17일 중국 상해 양산심수항에 위치한 전자동 스마트항만을 두 눈으로 확인하며 사라졌다.
처음 입구에 들어섰을 땐 근로자들의 휴식 시간이거나 쉬는 날인가 싶었다. 드넓은 항만 부지 어디에도 도무지 사람이 보이지 않았기 때문이다.
그러나 야드를 빽빽하게 채운 대형 크레인들은 느린 속도로 계속해서 컨테이너를 옮기며 쉬는 날이 아님을 보여줬다. 항만 끝의 갠트리(안벽) 크레인들은 부두에 정박해 있는 선박에 실린 컨테이너를 집어 올려 항만 안쪽 무인 이송차량에 적재했다.
커다란 평면 블록형의 무인 이송차량들은 ‘윙윙’ 소리를 내며 항만 내부에 있는 트랜스퍼(야드) 크레인 진영까지 컨테이너를 요리조리 일사불란하게 운반했다. 안벽크레인과 야드크레인 사이를 움직이는 무인 이송차량(AGV)은 충돌 없이 가고 서고를 반복하면서 목표 위치를 최단거리로 이동한다고 한다.
1초에 6m를 움직일 수 있다는 설명이다. 한 번에 8~10시간 가동되며, 일본산 배터리 충전에는 2시간이 걸리는데 이 역시 자동으로 이뤄진다.
야드크레인들은 AGV 위에 얹힌 컨테이너를 잡아 올린 후 레일을 타고 이동하면서 레고처럼 정확한 위치에 차곡차곡 쌓았다.
이런 일련의 하역 과정 어디에서도 근로자라고는 한 사람도 보이지 않았다. 항만에서 컨테이너를 외부로 반출해가는 트럭의 운전기사가 반가웠을 정도다.
바로 중국이 최첨단을 자랑하는 양산항 4기 자동화부두의 모습이다.
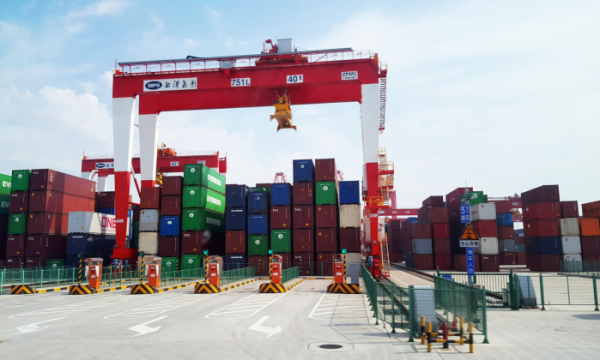
해양수산부에 따르면 글로벌 선박의 대형화 추세에 맞춰 지난해 말 개장한 양산항 4기 자동화부두는 부지면적 223만㎡로 서울 여의도(2.9㎢)의 약 77% 크기다. 총 사업비는 최대 140억 위안(약 2조4000억 원)으로 추정된다.
이곳은 7만 톤급 2개, 5만 톤급 5개 등 총 7개의 선석을 갖췄는데, 스마트폰 제조사로 유명한 화웨이에서 시스템을 설치했다. 연간 설계 물동량 하역 능력은 400만TEU(1TEU는 약 6m 컨테이너 1개) 규모로, 향후 630만TEU까지 확대한다는 계획이다.
아직은 개항 초기로 올해 예상 처리량은 170만~180만TEU 수준으로 예상됐다. 장비 확장과 통신 등 시스템 업그레이드를 통해 물동량 처리 속도를 높이는 게 관건이다.
터미널에는 현재 안벽크레인 10기, 자동레일식 야드크레인(RMGC) 40기, AGV 50대가 운영 중이다. 터미널 상황에 따라 안벽크레인 26기, RMGC 120기, AGV 130대까지 증설할 예정이다.
자동화부두를 둘러본 뒤 바로 옆에 있는 상해국제항만그룹(SIPG) 건물로 들어갔다. SIPG는 양산항 자동화부두의 투자‧운영 주체로 상해항 관리를 총괄하는 중국의 공공기관이다.
SIPG 내부에서는 젊은 직원들이 각자 책상 위 여러 대의 모니터를 보며 게임기 조이스틱 형태의 컨트롤러를 조작하고 있었다.
선박이 바다에서 심하게 흔들리기 때문에 안벽크레인만큼은 아직까지 완전한 자동화가 어렵다고 한다. 이에 사람이 직접 크레인에 탑승해 운전하는 대신 컨트롤센터에서 컨테이너 하역을 원격으로 조정한다는 설명이다.
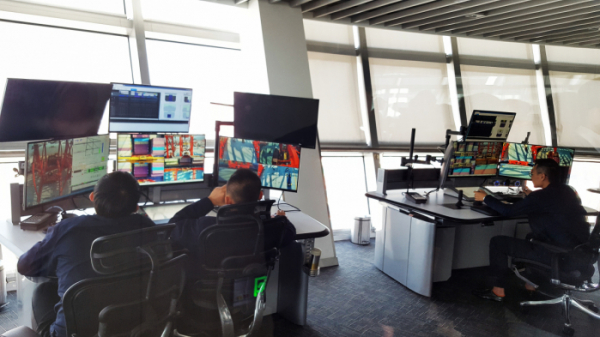
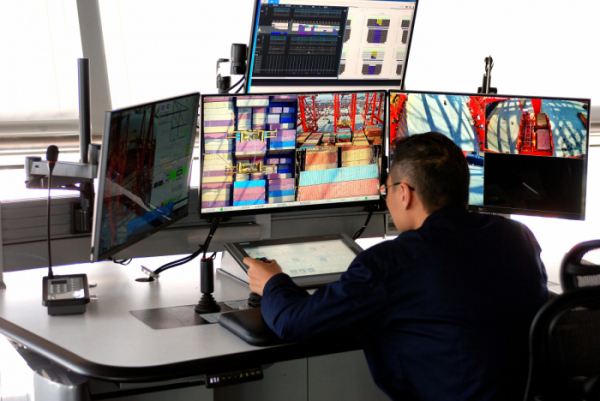
뤄쉰지에 SIPG 부총경리는 “예전에 탑승기사 1.5명이 크레인 1대를 맡았는데 지금은 자동화로 1명이 1대를 맡고 있다. 나중에 숙련이 되면 1명당 2대로 나갈 방침”이라고 설명했다.
이어 “현재 이곳은 1시간에 20개의 컨테이너 박스를 처리한다. 해외의 경우 한 시간에 26개 정도의 컨테이너 박스를 처리한다”면서 “전통적인 유인터미널과 비교하면 생산성이 아직 낮은 수준이지만 오퍼레이팅(시스템)이 업그레이드되면 전통 터미널보다 생산성이 높아질 것이라고 확신한다”고 강조했다.
그는 “과거 부산항을 2번 방문해 거기서 활용하는 자동화 (기술을) 봤었다”며 “우리가 배울 수 있었고 감사하게 생각한다”고 인사했다. 말하는 내내 ‘이제는 중국이 앞섰다’는 자신감이 역력한 표정이다.
우리가 IT 강국이라고 자부하며 항만 전자동화를 늦추는 동안, 한수 아래로 봤던 중국은 우리를 앞질러 세계를 선도하는 위치로 올라가 있었다. 부산신항과 인천항 등 한국의 항만은 아직 반자동화 수준으로 안벽크레인에 사람이 타고, 컨테이너 운송도 근로자가 야드트랙터를 운전해 실어 나른다.
하지만 4차 산업혁명 시대에 모든 분야가 그렇듯, 스마트항만은 좋든 싫든 시간문제로 도입이 불가피한 게 현실이다. 늦으면 늦을수록 빠르게 혁신하는 선두와의 기술 격차가 벌어지고 경쟁력이 떨어져, 추격하는 데 더 오랜 시간이 걸리는 수순이다.
다음 날인 18일 중국 정부의 적극적인 지원에 힘입어 세계 1위 항만자동화장비 기업으로 성장한 상하이전화중공업(ZPMC)을 방문했다. ZPMC는 첨단 기술을 망라해 양산항의 AGV와 자동크레인 등 장비의 하드웨어와 소프트웨어를 개발한 곳이다.
야드트랙터가 필요 없는 전자동 터미널 하역시스템인 AGV는 이 회사의 자랑이다.
장지안 ZPMC 부총재는 “터미널이 관심을 갖는 것은 투자 회수 부분인데 AGV를 통한 운송은 원가가 높다”며 “전자동 터미널의 수요가 갈수록 증가하고 있어, 일정한 수요가 있다면 단가는 낮아질 것이다. 싱가포르 터미널도 AGV 시스템을 채택하고 있다”고 설명했다.
이어 “새로운 AGV와 무인 트레일러도 연구개발 중”이라며 “올해 연말에 무인 트레일러가 상용 투입될 예정이다. 유인 운송시스템과의 격차는 더욱 좁혀질 것”이라고 자신했다.
귀국하는 길. 마음이 편치 않다. 출국 때의 의심은 위기감으로 변해 있었다.
우리 항만업계가 노사정 타협으로 합력해 스마트 기술 고도화에 속도를 내길. 수년 후 중국이 다시 한국의 항만 기술을 배우러 부산에 오는 본래의 제자리를 되찾길. 기도하는 심정으로 고국을 향했다.
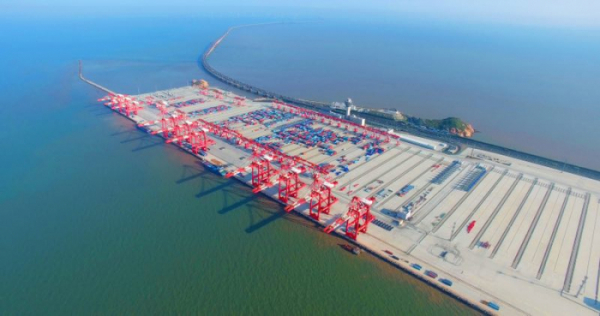