각기 다른 4만5133개의 외장패널… ‘세계 최대 3D 비정형건축물’로
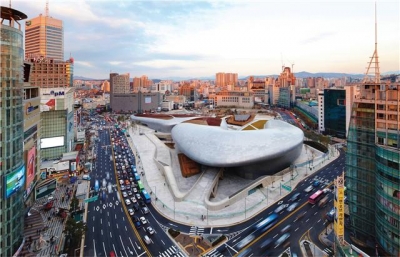
DDP 설계의 핵심인 비정형 외장 알루미늄 패널은 총 4만5133장으로 각 패널의 곡률ㆍ크기ㆍ형태가 어느 것 하나 같은 게 없다. 기존 방식대로라면 4만5000개가 넘는 형틀을 제작해야 한다는 뜻이자 정해진 공기 내에 해결이 불가능함을 의미했다. 삼성물산은 DDP 외관을 장식할 이 외장패널의 제작·생산 방식부터 해결해야 했다. 애초에 기존 공사 방식으로는 시공이 불가능한 이 설계를 위해 직원들은 유럽과 아시아를 뛰어다니며 발품을 팔아야 했다.
삼성물산 직원들은 2010년 2월 선진국의 건축 사례를 통해 첫 고비를 해결할 수 있을 것이라는 기대감을 안고 자하 하디드에게서 소개받은 영국 폼텍스와 독일 에베너를 찾아갔다.
그러나 9000km를 날아간 방문단은 실망감을 감추지 못했다. 먼저 방문한 폼텍스는 비정형 외장패널을 2가지 방법으로 제작했지만, DDP 패널을 만들기에는 크기와 방식 등에 있어 모두 부적합했다. 또 폼텍스의 제작품은 국내 업체들도 충분히 제작할 수 있는 수준의 패널이었다. 실망감은 독일에서도 계속 됐다. 그 곳은 패널을 수작업으로 작업하는 곳으로 패널을 직접 두드리고 용접해 장인정신을 엿볼 수 있었지만, DDP 패널 제작에만 20년의 시간을 보낼 수는 없었다. 특히 이 업체의 대표 건축물인 메르세데스 벤츠 박물관을 직접 찾은 결과 이 건물에는 비정형 2차곡면이 극히 일부에 적용돼 수작업이 가능했다는 점을 알아냈다.
기차 3등칸에서 새우잠을 자며 빡빡한 일정을 소화했던 이들은 결국 아무것도 얻지 못한 채 돌아왔다. 해결은 중국에서 가능했다. 중국의 한 대학 연구소가 대형 선박 선수 하단의 곡면판을 성형하는 장비를 연구 중에 있었던 것이다. 회사 측은 이 연구소를 찾아가 6개월 협의 끝에 다점성형프레스 장비를 완성할 수 있었다.
다점성형프레스는 BIM 데이터를 장비가 인식해 수많은 핀이 움직여 형틀을 자동으로 제작해 패널을 찍어내는 장비다. DDP와 같이 모든 패널의 형상이 다를 경우 소요되는 어마어마한 제작 기간과 비용을 획기적으로 줄일 수 있고, BIM 데이터로 패널을 찍어내 형상의 정확도 역시 높일 수 있었다.
삼성물산은 이어 아직 풀지 못한 숙제였던 패널 타공과 절단을 해결하기 위한 장비를 추가로 개발해야 했고, 자동차 제작에 사용하는 다관절 절단 기술도 도입했다. 삼성물산이 이처럼 DDP 외장패널 제작 방법을 완성하는 데만 2009년 9월~2011년 4월까지 총 1년 6개월이 걸렸다. 당초 회사 안팎에서는 20년이 걸릴 것으로 우려했다.
김현호 당시 DDP 현장소장은 “처음 외장패널 공사는 주변에서 ‘과연 이 공사를 해낼 수 있을까’라는 우려 속에서 시작된 게 사실”이라며 “까다롭기로 소문난 설계자인 자하 하디드가 ‘환상적이다’라는 표현을 했다고 들었다”고 말했다. 자하 하디드는 공사 초기 국내 건설사들의 기술력 수준을 운운하며 높은 콧대를 자랑했지만, 결국 DDP 외장패널에 감탄을 금치 못했던 것으로 알려졌다.
공사기간 7년 간 DDP 공사현장은 한 순간도 쉬웠던 적이 없다고 한다. 세계 최대 3차원 비정형 건축물은 직원들의 피와 땀을 담고 그 위용을 세상에 드러냈다.